English | हिन्दी
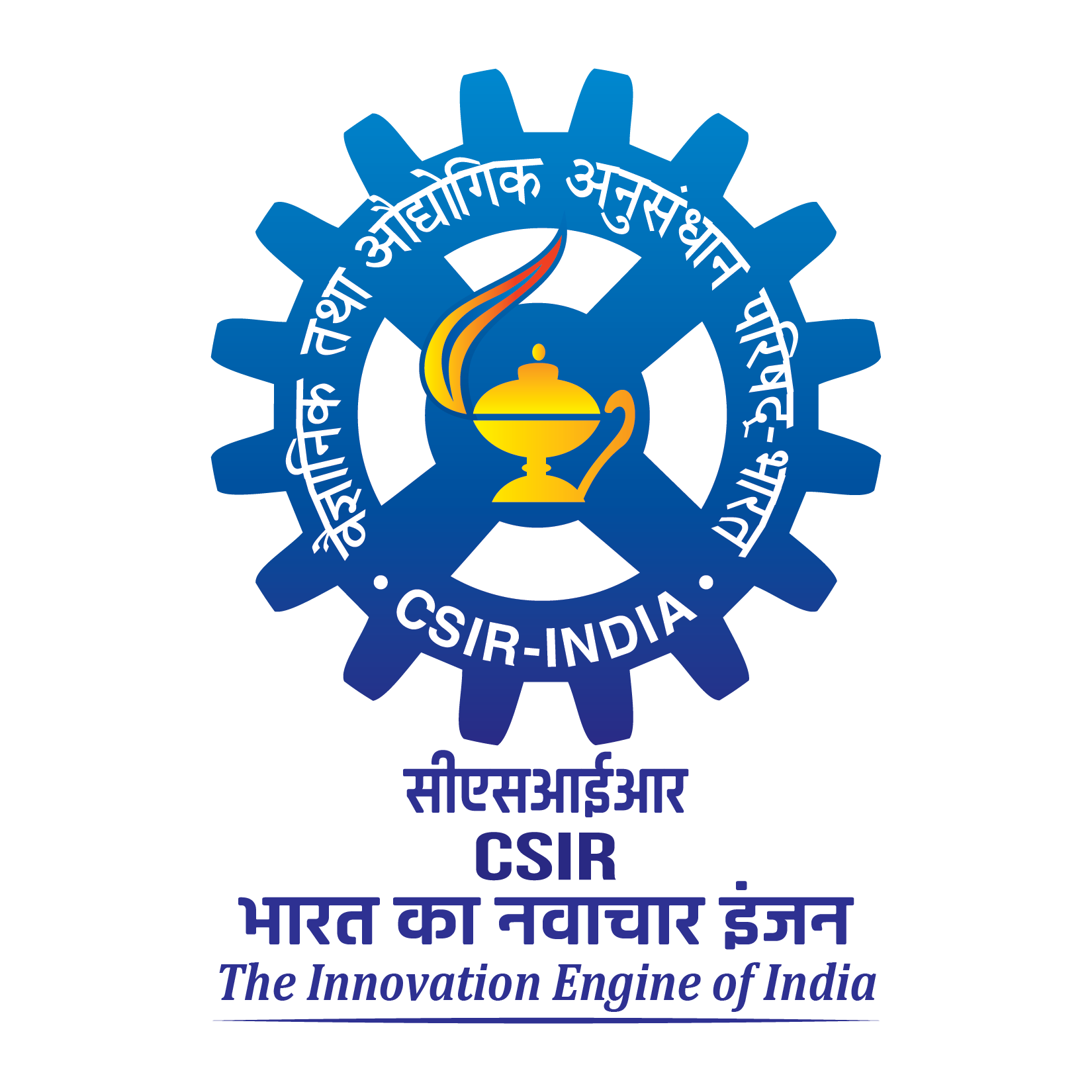
সিএসআইআর-কেন্দ্রীয় কাঁচ ও সেরামিক গবেষণা সংস্থা
सीएसआईआर-केंद्रीय काँच एवं सिरामिक अनुसंधान संस्थान
CSIR-Central Glass & Ceramic Research Institute
"Innovation in Ceramics and Glass for the mankind"
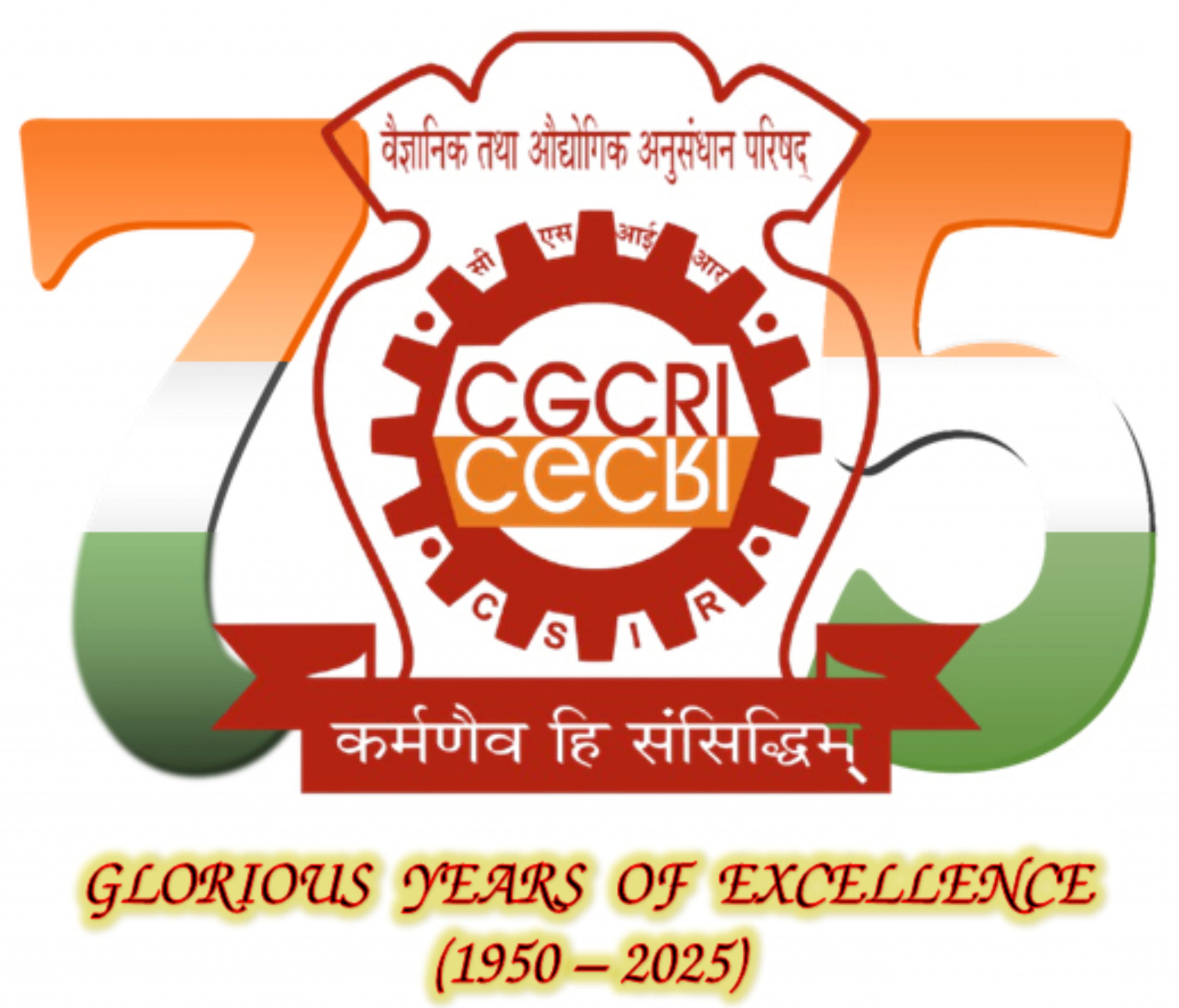
Advanced Ceramics & Composites
Overview
Advanced Ceramics and Composites Division (ACCD) focuses on cutting edge research and development of technology for various advanced ceramics and composite materials. The division focuses on development of products for wide spectrum of industrial, aerospace, defense, and energy sector for applications like clutch plate, brake pad/disc, hydrogen storage, thin film sensors, photo/electro catalyst, etc. The research team develops diverse materials like silicon carbide, silicon nitride, SiAlON, AlN, h-BN, MAX phases, MXenes, ultra high temperature ceramics, carbon fiber reinforced ceramic composites, and polymer derived ceramic modules. The division has conventional and advanced materials manufacturing facilities like bulk and thin film ceramic processing techniques through hot press, spark plasma sintering, hot isostatic press, and chemical vapor deposition with sophisticated characterization facilities. The development of products having desired technology readiness level is backed by advanced machines like hard turning machine, electrical discharge machining, vertical machining center, laser assisted diamond turning machine, surface grinding machine, micromachining, additive manufacturing and metrological machines like high resolution surface, form & roughness, and coordinate measuring machines. The division integrates basic materials science, high-end engineering and computational modeling of materials with dedicated team of scientists and technical staff. The division also collaborates with premium agencies such as DRDO, ISRO, DAE, etc. for the development of cutting edge advanced products based on structural ceramics and composite materials.
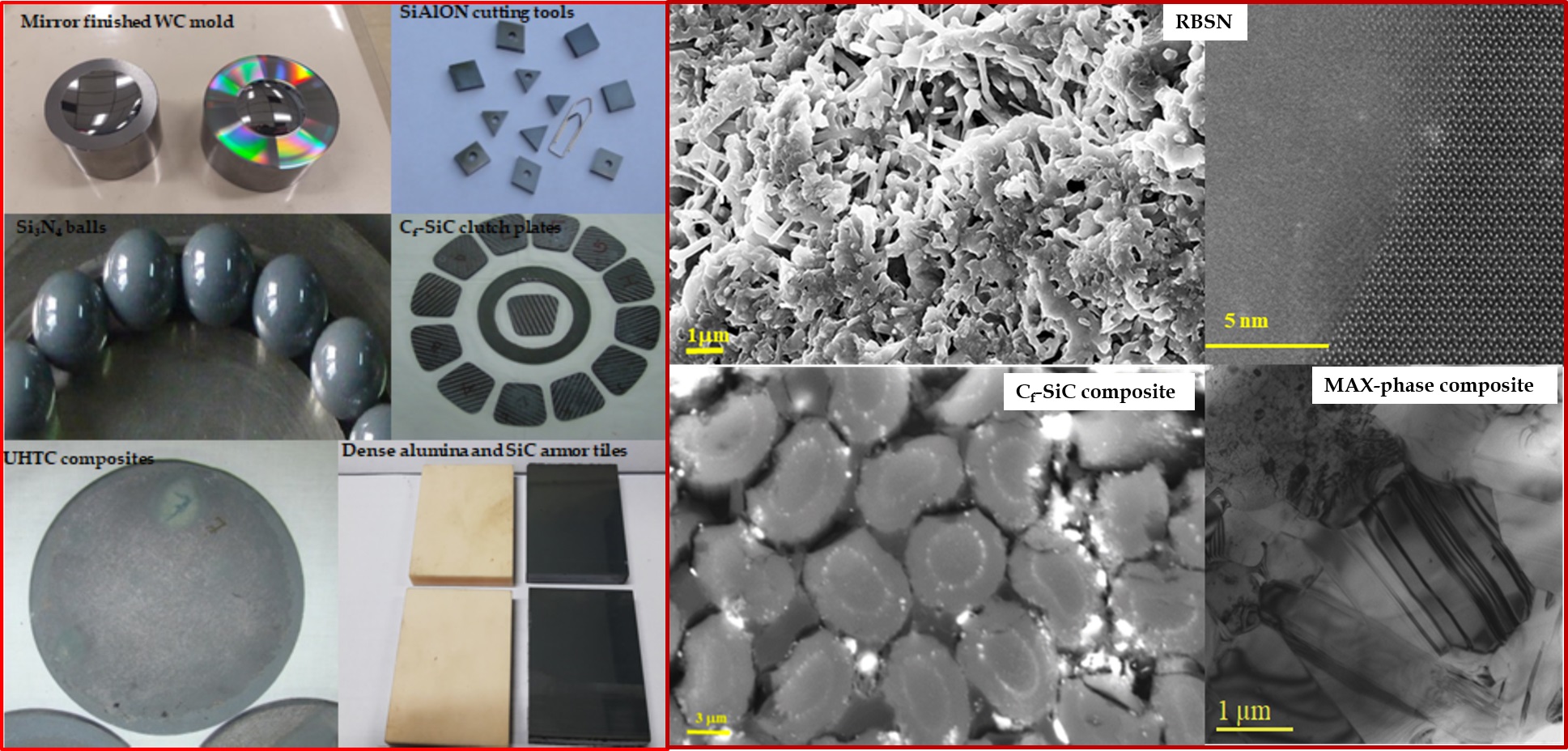
Areas of Research
- Processing of advanced ceramic and composite materials: Processing activities include processing of super hard ceramic using both conventional (slip casting, powder shaping and sintering) and non-conventional (additive manufacturing) of SiC, Si3N4, B4C, TiC, SiAlON and AlON ceramics, UHTC composites, MAX phase ceramics, Cf-SiC, Grpahene-metal & ceramic composites, ceramic matrix composites (CMCs), AlN and high entropy ceramics for strategic, structural and energy applications. Processing of ceramic thin films and coating from pre-ceramic precursor using CVD methods, like SiC, SiOxCy and coating for cutting tool applications are also one of the key focus areas of the advanced ceramics and composite divisions. Processing of nanomaterial synthesis by sol-gel based wet-chemical methods for waste water treatment and catalytic application is another activity of ACCD. Utilization of agro- and industrial wastes toward value added products is the new activity of the division. Divisions also try to build up expertise in the area of computational material design.
- Advanced machining: Division also engages in fabrication of components from brittle and hard materials made by advanced machining facilities like abrasive water jet machining, precision grinding and polishing, CNC machining lathe, vertical milling machine, laser assisted ductile mode machining, and, near-net-shaping of precision optics glass lenses.
- Characterizations: ACCD further looks into characterization of mechanical behavior, structural, thermal, opto-electronic behavior of materials along with development of structure-property correlation. Typical examples are mechanical behavior of materials from room to high temperature using universal testing machine, micro to nanohardness, high temperature nanoindentation, oxidation studies, wear and friction behavior at ambient and controlled environment with temperature dependence study, spectroscopy studies and microstructural characterization.
Technology Developed
- Dense silicon nitride and sialon wear resistant components
- Reaction bonded silicon nitride components
- Hexagonal boron nitride powder
- Dense reaction bonded silicon carbide composite materials (covered by : Indian Patent, 226270, 16 December, 2008)
- Carbon fibre reinforced silicon carbide components
- Biomorphic SiC ceramic composite materials
- Porous SiC ceramics
- SiSiC ceramic composite using processed bio-precursors
Projects
Ongoing Projects
Sl. No |
Title of the project |
Duration |
Sponsoring Agency |
Principal Investigator |
Co-Principal Investigator(s) |
Budget (lakhs) |
1 |
Technology Development on Fabrication of RBSN EM Window for Strategic Applications |
20 Sept, 2022 – 9 Sept, 2024 (2 years |
CSIR (FTT) |
Mr. Ajitesh Kar |
Dr. Milan Kanti Naskar |
185 |
2 |
Development of Cf/SiC ceramic matrix composites (CMCs) for Aircraft Brake Disc Applications |
02.02.2022 to 31.03.2025 (3 years) |
CSIR (Mission Mode) |
Mr. S.Gangadharan |
Mrs. Soma Hansda |
180.68 |
3 |
High Entropy Alloy for Hydrogen Storage Applications at Room Temperature (HEART) |
April 2022-September2024 (2 years) |
CSIR (H2T mission mode)
|
Dr. Soupitak Pal |
Dr. N.C. Pramanick, Dr. Sandip Bysakh. |
60 |
4 |
Advanced Manufacturing of Nanofinished Ceramics and Hard Alloy Components by Laser Assisted Ductile Mode Machining |
17.02.2020 to 31.03.2023 (3 years) |
CSIR 4M |
Mr. S.Gangadharan |
Dr.Yuvaraj Natarajan
|
50 |
5 |
Development of Hot Iso-statically pressed Silicon Nitride Ball: Technology for Hybrid Bearings of Aircraft Application” |
2 years (2022 – 2024) |
CVRDE, DRDO |
Dr. Rajat Banerjee |
Mr. Ajitesh Kar |
39 |
6 |
Functionalization of Red Mud for Simultaneous Remediation of Fluoride, Arsenic and Iron Contaminants from Water and Utilization of Waste Sludge Therefrom in the Development of Glass-Ceramic Foam |
30 Dec 2020-29 Dec 2023 (3 years) |
SERB |
Dr. Milan Kanti Naskar |
Dr. Shirshendu Chakraborty |
34.14 |
7 |
Fabrication of high temperature Piezo Pressure Sensor for Aeronautical Application |
3 years (2023 – 2025) |
ARDB, DRDO |
Dr. Rajat Banerjee |
Mr. Ajitesh Kar |
32 |
8 |
Ultra precision ductile mode machining of Ultra hard ceramics for advanced technology applications
|
2024-2026 (2 years) |
SERB |
Dr. Yuvaraj Natarajan |
Dr. Swati Jha, Mrs. Soma Hansda
|
29.17 |
9 |
3D Printing of polymer derived ceramics for making complex structures of ceramic optics |
2024-26 (2 Years) |
CSIR |
Dr. Yuvaraj Natarajan |
Dr. Soupitak Pal, Mr. Nelson Kandulna |
20 |
10 |
“Bioinspired Novel siAloN-Graphene Composites: A plausible Alternative of Hard wc-co composite” |
2024-26 (2 years) |
CSIR |
Dr. Soupitak Pal |
Mr. Ajitesh Kar, Mrs. Soma Hansda |
20 |
11 |
Processing of Cf-SiC-ZrB2 UHTC Ceramic Matrix composite by liquid silicon infiltration (LSI) Technique |
2024-26 (2 years) |
CSIR |
Mr. S. Gangadharan |
Dr. Soupitak Pal, Dr. Swati Jha |
20 |
12 |
Atomic scale surface generation on AlN ceramics for advanced functional surface applications |
2023-2024 (1 year) |
CSIR-CGCRI |
Dr. Yuvaraj Natarajan |
Mr. S. Gangadaran |
2 |
13 |
Development of ternary TiN/TiMN (M: V, Nb, Ta) hybrid coatings for space and automotive applications |
2024-2025 (1 year) |
CSIR-CGCRI |
Dr. Swati Jha |
Dr. Yuvaraj Natarajan |
2 |
Divisional Facilities
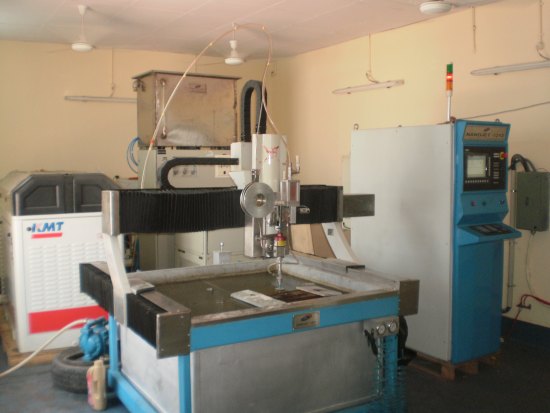
![]() FTIR |
![]() Sputter Coating unit |
![]() Vacuum Oven for inflammable Solvent |
![]() Thermal Diffusivity measuring instrument |
![]() Spark Plasma Sintering Furnace |
![]() Hot Isostatic Press |
![]() High Temperature (2000oC) Brazing Furnace with Tungsten Heating Element |
|
![]() SCHAUBLIN, 225 TMI-CNC turning machine |
|
![]() VF-1 HASS VMC (Vertical Milling Machine) |
|
![]() Zeta Sizer |
![]() Particle Size Analyzer |
![]() 1500 W Ultrasonic Unit |
![]() Rheometer |
![]() Attritor |
|
![]() UV Spectrometre |
![]() Non Contact Profilometre |
![]() Flurimetre |
![]() Inverted Optical Microscope with CCD camera with Image Analyzer |
![]() Humidity controlled drier |
![]() High temperature controlled atmosphere furnaces (2000OC) |
![]() High speed Centrifuge of M/S Remi(Max RPM=20000, RCF 37570) 4×100 ml angle head |
![]() Planetary mill (1600 watt) |
![]() Hi temperature electrically heated furnace of chamber size 200mm×200mm×200mm max temp 1800oC |
![]() 100 Watts Ultrasonic processor |
![]() Ceramic ball lapping machine |
![]() Micro hardness tester (2 kg) |
![]() Contact type surface profilometer |
![]() High temperature Hot Press (2200C, 40 Ton) |
![]() Precision Surface Grinding Machine |
![]() Triboindenter (Nanoindenter with in-situ SPM facility) |
![]() Fischerscope (Nanoindenter with Optical facility) |
![]() Scratch Tester |
![]() Hardness Tester (Vicker’’s and Knoop tip) |
![]() Fully Automated Universal Testing Machine (1 KN, 100 KN, 100 N load cells) |
Scientists
Mr. S. Gangadharan, Senior Principal Scientist and Head
Dr. Shirshendu Chakraborty, Principal Scientist
Mr. Ajitesh Kar, Principal Scientist
Dr. Soupitak Pal, Senior Scientist
Dr. Eranezhuth Wasan Awin, Senior Scientist
Ms. Soma Hansda, Scientist
Dr. Yuvaraj Natarajan, Scientist
Technical/Support Staff
Name | Designation | Expertise |
![]() |
Senior Technical Officer – III |
Pressureless & Pressure-assisted Sintering under Controlled Atmosphere, Pre-ceramic polymer derived Open/Closed Cell Carbide Ceramics, Ceramic Matrix Based Composites Reinforced with Non-oxide Based Nano-structures, Chopped Micro-Fibres & Particulates, Tribo-mechanical characterizations, Nano indentation, Fractography, Processing-Microstructure-Property Relationship
|
![]() |
Senior Technical Officer-II |
Operation of furnace, advanced characterization instruments like thermal analyzer, high temperature dilatometer. Maintenance of electrical parts of instruments, computer software useful for different machines and programming. |
![]() |
Senior Technical Officer-I | Operation and maintenance of high temperature controlled atmosphere furnace, chamber furnace, spark plasma sintering furnace, hot isostatic pressure furnace. Expertise in thermal conductivity measurement and sputtering. |
![]() |
Senior Technical Officer (1) | CNC Milling, Nano Indentation, Co-ordinate Measuring Machine, Universal Testing Machine, Surface roughness tester, CAD-CAM. |
![]() |
Senior Technical Officer (1) |
Operation of CNC Turn Mill Centre, Surface Grinding Machine, Wire EDM, Vertical Milling Centre, Ultra Precision Lathe with Laser Assisted Machining (LAM). Design, Drawing and manufacturing of Precision moulds and components using CAD-CAM softwares like SOLIDWORKS, AutoCAD, CAMWorks, CADMAcRO, DIFFSYS etc. Operation of NDT testing machine X-Ray Mico CT. |
![]() |
Technical Assistant | Operation and maintenance of high temperature controlled atmosphere furnace, chamber furnace, spark plasma sintering furnace, Vacuum Arc melting Furnace. Electrical maintenance. |
![]() |
Technician-II | Operation and maintenance of high temperature controlled atmosphere furnace, chamber furnace, spark plasma sintering furnace, hot isostatic pressure furnace. Specialisation in instrumentation. |
![]() |
Technician-II |
Ceramic powder preparation, slip casting and characterisation of ceramic samples. Operation of Rheometer, particle size analyser and surface area analyser. |
![]() |
Technician-II | Operation of Precision Surface Grinding and machining using computer aided CNC turning machine, and Abrasive water jet machining. |
![]() |
Technician-II | Operation and maintenance of furnaces. Electrical parts maintenance. |
![]() |
Technician (1) | Expertise in machining & mechanical Testing. |
![]() |
Technician (1) | Operation and maintenance of high temperature controlled atmosphere furnaces, spark plasma sintering furnace, hot isostatic pressure furnace and Vacuum Arc Melting furnace. Operation of Electrospinning, Rheometer, pH meter etc. |
Scholars/Students
Name | Designation |
Project Title/code |
Supervisor |
![]() |
Senior Project Associate |
Development of Hot-Iso-Statically Pressed Silicon Nitride Ceramic Balls: Technology for Hybrid Bearings of Aircraft Applications
Project code: SSP-0223 (CVRDE-DRDO) |
Dr. Rajat Banerjee |
![]() |
Project Associate-I |
Development of Cf/SiC Ceramic Matrix Composites for Aircraft Brake-Disc Applications
Project code: HCP-0036 (CSIR Mission Mode) |
Mr. S. Gangadharan |
![]() |
Project Associate-I |
Development of Cf/SiC Matrix Composites for Aircraft Brake-Disc Applications
Project code: HCP-0036 (CSIR Mission Mode)
|
Mr. S. Gangadharan |
![]() |
Project Associate-I |
Development of High-Entropy Alloys Operable at Room Temperature for Hydrogen Storage Project Code: HCP44(WP-3) (CSIR-H2T mission) |
Dr. Soupitak Pal |
![]() |
Project Associate-I |
Development of RBSN-EM window Project Code: MLP0206 CSIR-FTT |
Mr. Ajitesh Kar |
![]() |
JRF
|
Ultra precision Ductile Mode Machining of Ultra Hard Ceramics for Advanced Technology Applications
Project code: GAP-0275 (SERB)
|
Dr. Yuvaraj Natarajan |
![]() |
Project Assistant |
Development of Cf/SiC Matrix Composites for Aircraft Brake-Disc Applications
Project Code: HCP-0036 (CSIR)
|
Mr. S. Gangadharan |
Summer Intern
Name | Institute | Session | Supervisor |
Ms. K Gowri Priya | IIT Jammu, Jammu | May, 2024 to July 2024 | Dr. Swati Jha |
Mr. Bisanka Kisor Ray
|
Visvesvaraya National Institute of Technology, Nagpur
|
May 2024 to July 2024 | Mrs. Soma Hansda |
Contact
Mr. S. Gangadharan,
Senior Principal Scientist
Head, Advanced Ceramics & Composites Division
Phone: (033) 23223516
Fax: +91-33-24730957
E-mail: sganga@cgcri.res.in
Last Updated on June 11, 2025