English | हिन्दी
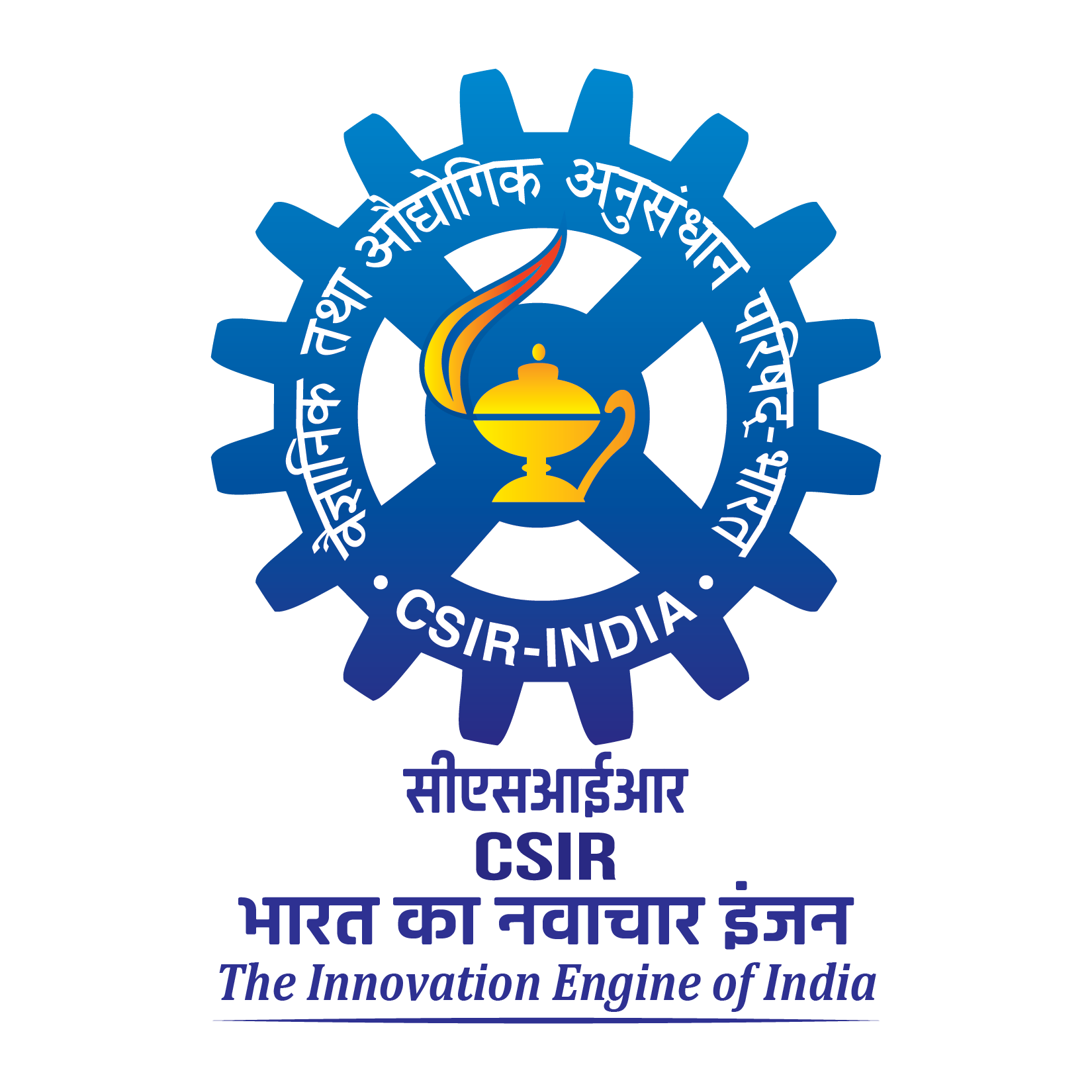
সিএসআইআর-কেন্দ্রীয় কাঁচ ও সেরামিক গবেষণা সংস্থা
सीएसआईआर-केंद्रीय काँच एवं सिरामिक अनुसंधान संस्थान
CSIR-Central Glass & Ceramic Research Institute
"Innovation in Ceramics and Glass for the mankind"
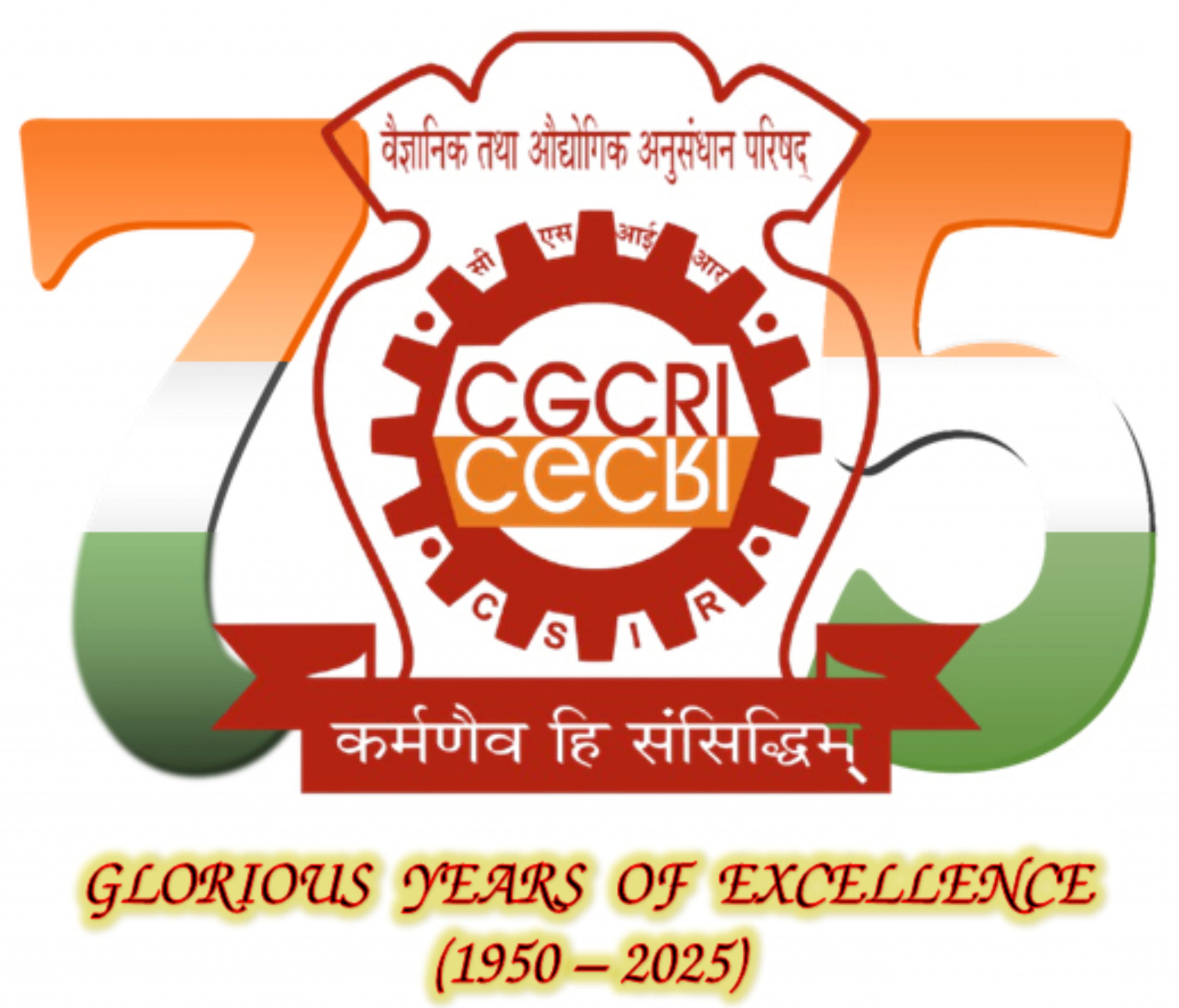
Specialty Glass
Overview
Since the inception of this Institute, Specialty Glass Division (SGD) has been serving the country with a mandate to develop specialty glasses and their manufacturing technology for civil and strategic applications. The Division also extending services to the country’s glass industry in lab-scale trial melting, testing and quality assurance of their products in line with the mission and vision of this institute. The activities of SGD spans from basic R & D for development of specialty glasses to pilot scale production of few varieties of glasses where demand is very limited due to strategic in nature. To meet with the countries demand, at the initial post-independence period, developed various application oriented specialty glasses namely many varieties of optical glasses in a pilot scale facility, colored signal glasses, radiophotoluminescent (RPL) glasses, filter glasses etc. Later on many new glasses such as new generation lanthanum bearing optical glasses, rare-earth doped luminescent glasses, micronutrient glass fertilizers, graded refractive index (GRIN) glasses, fullerene (C60)/CNT doped glasses, tellurite glasses, fluorophosphate glasses, lead-free environmentally friendly, low cost glass powders and pastes for new generation of Plasma Display Panels (PDP) etc. have been developed.
After the 1990s, many sanctions were imposed on the country, and supply of radiation shielding window glasses (RSW) and laser glasses were denied, that necessitated indigenous development of such glasses to support India’s atomic energy missions. In his endeavours varieties of RSW glasses and laser glasses were developed at the pilot scale facility established at the Institute and supplied to the Department of Atomic Energy (DAE). The need to immobilize high level radio-active liquid waste (HLW) were met through indigenous development of glass bead technology to immobilize HLW.
Currently, the Division is engaged to address issues of various sectors such as strategic, societal, industrial problems and crucial sustainability issues like energy and environment through various R & D activities.
Current Activities
Today, SGD focuses on addressing challenges across strategic, societal, and industrial sectors while tackling critical sustainability issues related to energy and the environment through various R&D initiatives.
- Strategic Sector: SGD is actively engaged in developing technologies for producing space-grade optical glasses, Nd-doped laser glass for high-energy, high-power applications, edge-cladding glass to prevent parasitic oscillations in laser glass, radiation shielding window glasses for nuclear hot cells, borosilicate glass beads for nuclear waste immobilization, chalcogenide glasses for thermal imaging, and transparent glass-ceramics for armor applications.
- Societal Sector: The division is focused on process technologies for synthesizing transparent nanocrystalline high-strength glass-ceramics for display applications, ferroelectric glass-ceramic nanocomposites for energy storage, and bioactive glasses for bone graft applications. Additionally, an advanced architectural glass testing facility has been established to support Glass industries.
- Energy & Environment: SGD has significantly emphasized energy efficiency and environmental sustainability, aligning its activities with the United Nations’ Sustainable Development Goals (SDGs). Current projects include developing technologies for recycling c-Si PV module cover glass, utilizing toxic waste in glass manufacturing, producing glass foam for insulation and construction to enhance energy savings, adopting microwave heating for energy-efficient glass melting, creating phosphor-in-glass (PiG) composites for thermally stable white LEDs, developing thermally cyclable sealant glass for solid oxide fuel cells (SOFCs), and applying hydrophobic and anti-reflective sol-gel coatings on PV solar cover glass for enhanced performance.
- Simulation and data driven approach in Glass design: Molecular dynamics (MD) is a computational method used to simulate the behavior of atoms and molecules over time, based on the principles of classical mechanics. It has become an invaluable tool in materials science, particularly in the design and understanding of glasses. Glasses, unlike crystalline solids, lack a regular atomic structure and are typically amorphous, which makes their design and behavior much more distinct and challenging compared to conventional materials. By combining atomic-level structural insights from MD with data-driven methods (Artificial intelligence and Machine Learning), it becomes possible to identify non-linear patterns between structure and properties, enabling smarter and more accurate predictions. SGD is currently working on this direction by collaborating with experimental researchers.
- Industry Collaboration: As a CSIR laboratory, SGD actively collaborates with the glass industry to address sector-specific challenges. Industry-funded projects include the development of hydrophobic coatings for interior-use flat glass and corrosion studies of refractory pots for sodium lime silicate (SLS) glass melting.
The state-of-the-art Architectural Glass Research & Testing Facility (AGRT) has been established under the initiative of SGD to assess the energy performance of architectural glass and glazing systems from leading glass manufacturers in the country. This facility provides third-party certification to ensure quality and reliability for end users.
SGD’s initiatives are aligned with the Government of India’s various national missions, contributing to the country’s goal of self-reliance in specialty glass technology and manufacturing. Recently, this Institute hosted the XXVII International Congress on Glass (ICG 2025) during 20-24 January 2025 in Kolkata for the 2nd time in India after 39 years. ICG-2025 brought together a vibrant global community of experts, industry leaders, and academicians. The event saw the participation of over 550 delegates, including 150 international attendees from 20 countries. Notably, the event fostered collaborations between academic institutions and industries worldwide, positioning India as a key player in the global glass research and technology landscape.
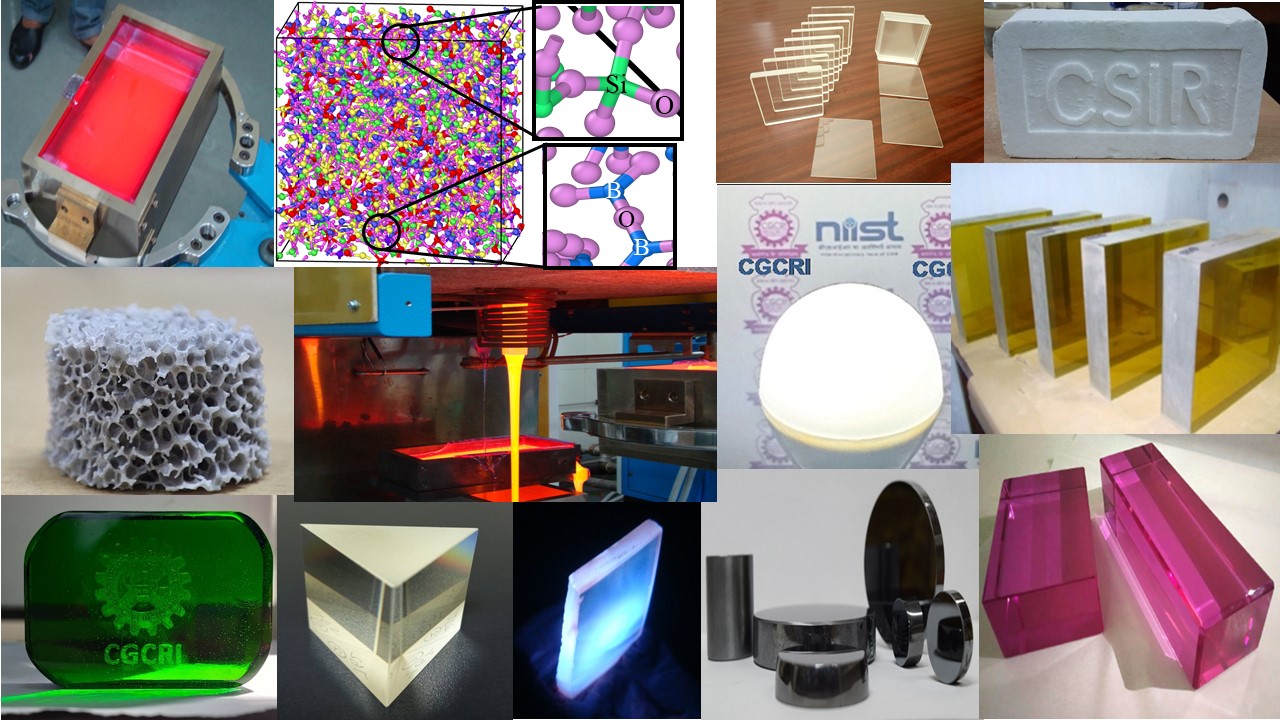
Last Updated on March 5, 2025